Understanding Chemical Mixing Tanks
Chemical Mixing tanks are large, specialized tanks, which are able to accommodate diverse chemicals, which upon mixing, can be in a homogeneous form. These tanks have different configurations and layouts and can be used effectively to mix liquids, powders or gases. Chemical mixing tanks on the other side are fundamental in the production of sanitation detergents, medicines or water treatment chemicals in any industries.
A regular chemical mixing tank can be said to be a cylindrical container into which an agitator is installed and with the contents containing liquids that need to be mixed uniformly. These tanks are available in different sizes, facilitating their use in various settings, ranging from laboratory tanks to industrial tanks. Therefore, it can be said that these tanks are important for ensuring uniform quality and safety when processing chemicals.
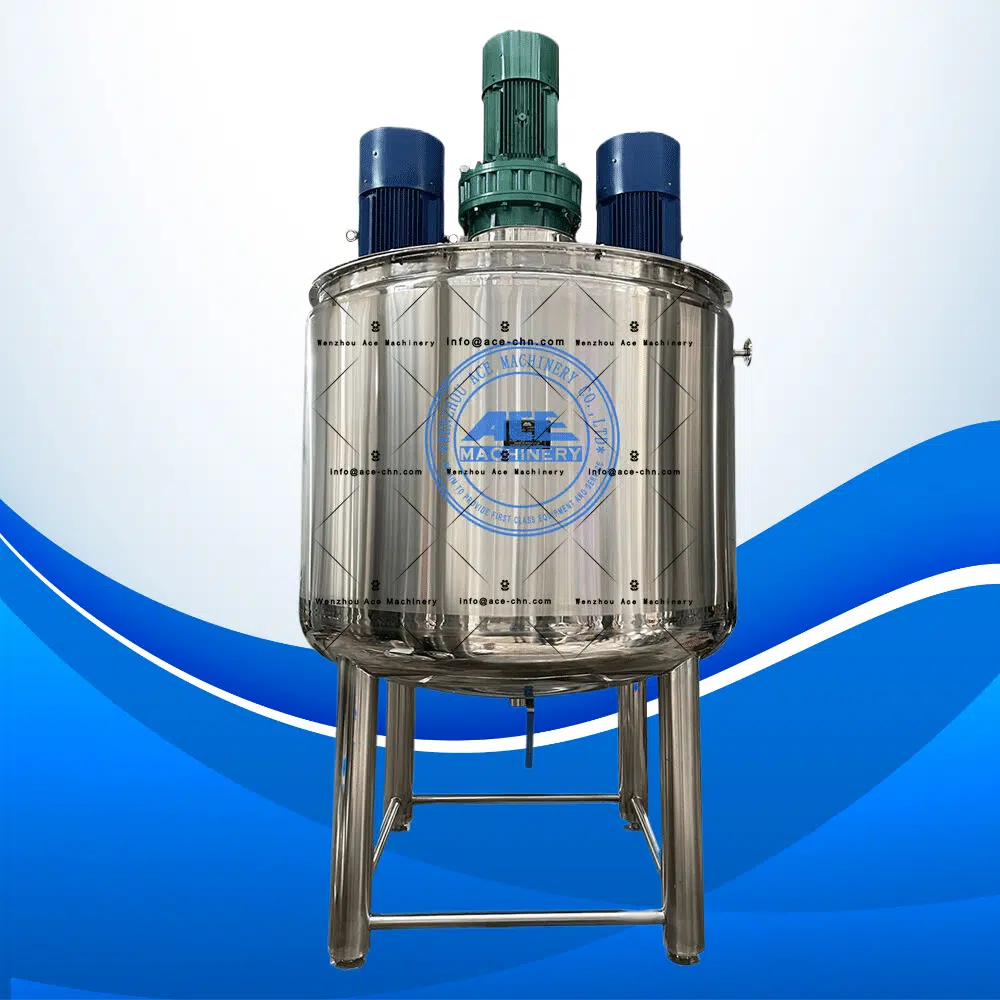
Industrial Mixing of Chemicals and Its Relevance
For any industry that deals with formulated chemicals, mixing tanks are an absolute must to provide assurance of product uniformity as well as safety. Some of the key industries that chemically use these mixing tanks include the following:
Chemical Production
This will include manufacturers of acids, bases, solvents, and resins that need thorough mixing to ensure safety and accuracy in formulations.
Pharmaceuticals
This will include drug manufacturing, which is controlled for drug ingredient proportions within stringent limits and done often in sterile facilities.
Food and Beverage
Chemical mixing includes the making of ingredients such as flavorings, preservatives, and coloring agents.
Cosmetics
Lattes, creams, or shampoo are prepared in specially designed mixing tanks for a uniform product design.
Integrating proper mixing procedures into routine activities can prevent the manufacture of inconsistent products, safety risks as well as excessive manufacturing costs.
The Major Elements/Tank of a Chemical Mixing Vessel
Moreover, there are certain common components that are found in a well-designed tank mixing and make the tank very efficient:
Tank Material Construction
Most often than not, the walls of a chemical tank mixer are made of stainless steel material, which is strong, non-corrosive, and simple in terms of cleaning. However, depending on the use of the tank, polyethylene and other specialized materials may be used.
Agitator
An agitator is an important part of the chemical mixing vessel. It is a mechanical device that rotates at a high speed in order to stir liquids in the container. According to the viscosity of the mixed material, these are powered by motors, and come in various designs such as propellers, paddles, or turbines.
Baffles
To improve mixing efficiency, baffles are static plates embedded within a tank’s interior, which serve to interrupt the movement of liquid within the tank and eliminate vortex motion.
Control Systems
Sensors, flow meters, and programmable temperature and pressure controls are some of the advanced features of new generation tanks.
Types of Chemical Mixing Tanks

An important point to note is that the chemical mixing tank’s volume and type will depend on the specific requirements of the industry. The important ones are:
Stainless Steel Mixing Tanks
These are the most popular choice for many industries due to their toughness and ability to withstand strong chemicals.
Polyethylene Tanks
These tanks are relatively simple as they are lighter, cheap, and resist several corrosive chemicals, which makes them better suited for applications involving lower temperatures.
Custom Tanks
Some applications may require customized tanks, which are built specifically for the handling of hazardous chemicals. Additional enhancements like pressure resistance and special coatings can also be made available.
Selection of a chemical mixing tank should, however, be depressed for the fact that every type of tank has its advantages depending on particular operational requirements.
Mixing Technologies in Chemical Tanks
Several mixing technologies are applied for the optimization of chemical mixing tanks:
Mechanical Agitators
These are the most common and include impellers and paddles which actively rotate the ingredients of chemicals.
Pneumatic Agitators
Pneumatic systems are driven by air. They are largely appropriate in applications where electricity may not be safe.
Magnetic Mixers
Utilizing a magnetic field for stirring substances minimizes the risk of contamination, which is beneficial to the pharmaceutical industries.
Different mixing techniques have different advantages, and the selection is largely influenced by the type of the material to be mixed, the tank size, and other requirements of a specific industry.
Applications of Chemical Mixing Tanks
The applications of chemical mixing tanks for mixing are rather numerous because virtually all industries that handle chemicals have some mixing at a stage in their processes. Some important applications include:
Chemical Composition
For the blending of acids, solvents, and other chemicals, but under a controlled environment.
Water Treatment
Application in flocculation, sedimentation, purification processes.
Pharmaceuticals
Guarantees nice distribution of all active components in medications.
Cosmetics
Assists in unifying mixtures to prepare creams, lotions, and gels.
This necessity emphasizes the roles that chemical mixing tanks play in ensuring the industry’s product is in compliance with standard, safe, and cheap.
Physical and Performance Parameters of Chemical Mixing Tank
Now, when it comes to choosing the right chemical mixing tank, there are a couple of check points that one has to look into:
Capacity
The tank should have enough volume for the production functions without using extra energy and space.
Chemical Composition
Most chemicals that are mixed together are always kept at high temperatures; therefore, the tank used should be resistant to corrosion or reactions with the chemicals being mixed.
Mixing Requirements
An important factor that determines both the type of atomizer and the rotating speed is the viscosity and (or) composition of the materials to be mixed.
Regulatory Standards
In industries such as food, pharmaceuticals, and water treatment, compliance with various regulations that exist such as the FDA, GMP or ASME standards is indispensable.
It is important to take into consideration such elements in order that firms can efficiently mix their products and guarantee reliability over time.
Advantages of Using a Chemical Mixing Tank
It is clear that the utilization of chemical mixing tanks comes with immense advantages:
Enhanced Product Consistency
Homogeneous mixing provides, so each lot of product meets quality requirements.
Increased Efficiency
Automated control systems integrated with optimized agitators help to save energy and reduce the mixing time.
Cost Savings
An appropriate size and shape of the tank will help to cut on wastage and lead to better economics of production.
Also, chemical mixing tanks can also be used by companies to comply with regulations to avert expensive recalls of products or the problems of disposal of products that cannot be used.
Customization Options for Chemical Mixing Tanks
Differences among these supports sometimes go back to the fact that some manufacturers provide customization to address particular industry prescripts: Customizations may include:
Shape and Size
Depending on the mixing process, tanks can be cylindrical, square, or even cone-bottomed.
Agitator Type
Depending on viscosity, the agitator can be selected for optimum mixing.
Additional Features
Controlled tanks may also feature heating or cooling jackets, insulation, or pressure for special processes.
Custom chemical mixing tanks allow advancement in efficiency and reduction in operational costs while meeting client-specific regulatory guidelines.
Practices for the Maintenance of a Chemical Mixing Tank
For chemical mixing tanks, appropriate maintenance may be beneficial in extending their service life as well as optimally functioning.
Cleaning Measures
Frequent cleaning eliminates the chances of cross-contamination, especially when changing processes from one chemical or product to another.
Maintenance Strategies
Periodic monitoring of seals, agitators, and control systems can prevent failure due to defects and aging of parts.
Enhanced Life Cycle Management
Proper tank storage, especially for those that are used on a specific routine, and compliance with the manufacturer’s instructions on usage and cleaning would help in extending the life of a chemical mixing tank.
Good maintenance guarantees safety during operations and increases lifespan for machinery, which shelters the organization from incurring high costs in the long run.